Why test shoes for harmful substances?
Footwear is usually worn for long periods of time and often comes into direct contact with the skin. During wear, shoes creates a warm and moist environment inside the footwear. Despite their long life, even shoes made from textile materials are rarely washed. In addition, they consist of many different components from a complicated supply chain.
Therefore, it is important that shoes do not contain harmful substances. Each component from the various stages of production represents a potential risk for harmful substances. They must also comply with legal requirements.
Which products do we test and certify?
In our independent, accredited laboratories, we test finished footwear (end products) and individual components of shoes (uppers, midsoles, outsoles, insoles, heel caps, etc.) according to OEKO-TEX® STANDARD 100.
Certification according to STANDARD 100 usually takes place if the shoes or individual components as a whole consist mainly of textile materials. If the largest part of the final product is made of leather, it is certified to OEKO-TEX® LEATHER STANDARD.
What are the benefits of STANDARD 100 certification for footwear?
For brands, retailers, manufacturers
- Reduced market risk
through compliance with legal requirements - Credible consumer communication
through an independent, globally recognized product label - Proof of human-ecological safety
through laboratory tests - Transparency and reduced certification costs
through the use of pre-certified source materials and components
For consumers
- Comprehensive and reliable safety
through globally standardized and annually updated test criteria, testing methods based on real-life use, control tests after certificate issue - Credibility and traceability
through validity checks of certified products
What makes STANDARD 100 certification of footwear unique?
The OEKO-TEX® STANDARD 100 certificate for footwear is only issued if all components comply with the required criteria of the STANDARD 100 Restricted Substances List - without exception.
A further requirement for certification is an on-site audit. In this way, we ensure that the company's quality assurance practices are suitable for complying with the required OEKO-TEX® criteria during ongoing production.
STANDARD 100 certification is based on a modular concept.
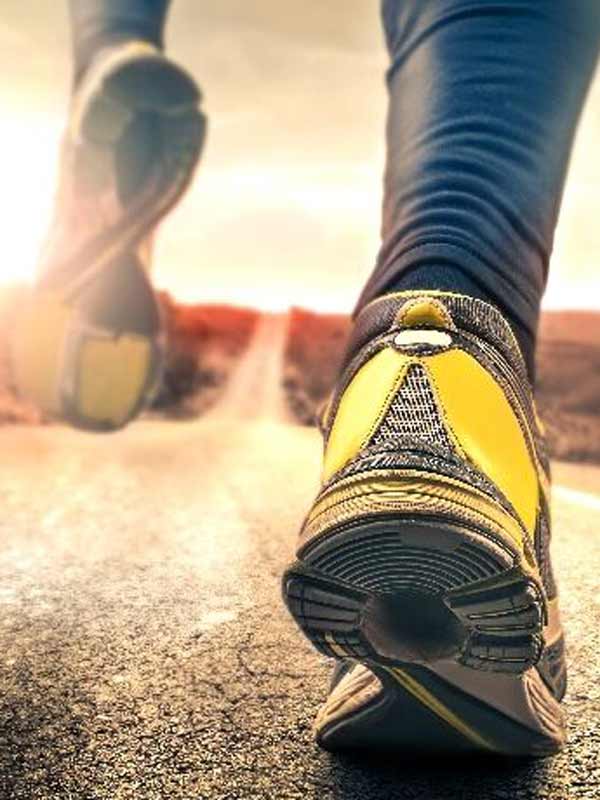
This principle offers convincing advantages, especially to brands, retailers and manufacturers of finished goods:
- Costs and responsibility for the human ecological safety of the certified end product are distributed across the supply chain
- By using STANDARD 100 certified components, you ensure that your products meet the legal requirements in all major consumer markets even before the production begins
- The OEKO-TEX® Buying Guide is free online directory for sourcing certified materials and components
- STANDARD 100 is an optimized tool for operational quality assurance without requiring in-company know-how and resources
- Product stewardship is always up to date with the annually updated OEKO-TEX® RSL - harmonized with international laws and industry initiatives